Vacuum Forming bliaster packaging products use a plastic processing process where flat plastic hard sheets are heated and softened, and then vacuum adsorbed on the surface of the mold. Vacuum formed products are widely used in the plastic packaging industry. A. The main advantages of vacuum forming blister packaging are:
1. saving raw and auxiliary materials, light weight, convenient transportation, and meeting the requirements of environmentally friendly and green packaging;
2. Able to Packaging any irregular products without the need for additional cushioning materials;
3. The packaged product is transparent and visible, has a beautiful appearance, is easy to sell, and is suitable for machinery Automated packaging facilitates modern management, saves manpower, and improves efficiency.
B. Blister packaging products mainly include: bubble shells, trays, blister boxes, and synonyms include: vacuum covers, bubble covers, etc. C. The blister packaging equipment mainly includes: blister packaging machines, blister forming machines, punching machines, sealing machines, high-frequency machines, and folding machines. D. The packaging products formed by packaging can be divided into: card insertion, card suction, double bubble shell, half bubble shell, half fold bubble shell, three fold bubble shell, etc. E. The production raw materials for blister packaging mainly include PVC, PS, PP, PET, PETG, and environmentally friendly materials such as flocking, anti-static, and conductive. F. Production Process of vacuum forming Blister Packaging 1. Mold manufacturing and processing: According to the requirements or sample standards, the first step is to manufacture the blister mold. Generally, gypsum is used to manufacture blister packaging Molds, but also products made of wood and metal carvings can be used as molds. After the gypsum mold is manufactured, it is first allowed to naturally dry thoroughly or dried, and then For the specific situation of the convex and concave appearance of the product, use a 1-2mm drill to drill many small holes in the low and concave areas that do not affect the packaging appearance of the product, such as packaging boxes For the product, it is necessary to drill some small holes on the nearby edges so that air can be extracted during the production of vacuum molding. After drilling the holes in the mold, the gypsum mold needs to be hardened The method of disposal and hardening is to soak in a concentrated alum solution and let it dry. 2. After the mold is completely dried, install it onto the upper iron plate of the vacuum chamber, and then load the plastic sheet into the applicable standard size according to the size of the mold, Then place this sheet material into a heated wooden cabinet to completely fix it, and then place the wooden cabinet and plastic sheet material on a constant temperature furnace for softening treatment. 3: Place the softened plastic sheets together with the wooden cabinet in the vacuum chamber, activate the suction switch, and suck out the air in the vacuum chamber. Wait for the plastic sheets to cool down. Later, you will receive the same concave packaging or technical mold as the mold. 4: Vauum forming Blister packaging and cleaning; Trimming and tidying up the produced goods is the finished product, which can be sold after packaging. 7. Main features: Good protection; Transparent and intuitive; Easy to use; Lightweight quality; Cheap price;
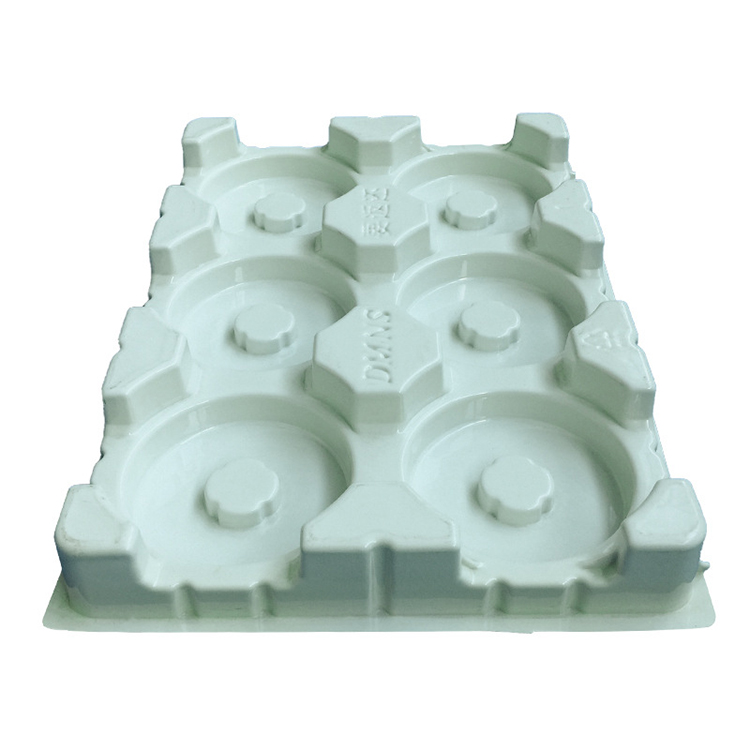